Manufacturing SchedulerAsprova APS
Asprova APS creates a work plan that spans multiple processes for orders.
On the planning desktop screen, you can visually display order-linked resource Gantt charts, order work Gantt charts, load graphs, and inventory graphs on the horizontal axis, which is often used in Japan, so you can make plan adjustments intuitively.
Overview
Asprova APS performs backward and forward scheduling using deadlines and priorities.
The planning desktop intuitively displays the start date violations, delivery delays, overloads, and in-process inventories between EPST (earliest possible start time) and LPST (latest possible start time), and adjusts the schedule with a mouse click. Necessary information is displayed in a pop-up window by hovering the mouse over it, allowing quick actions.
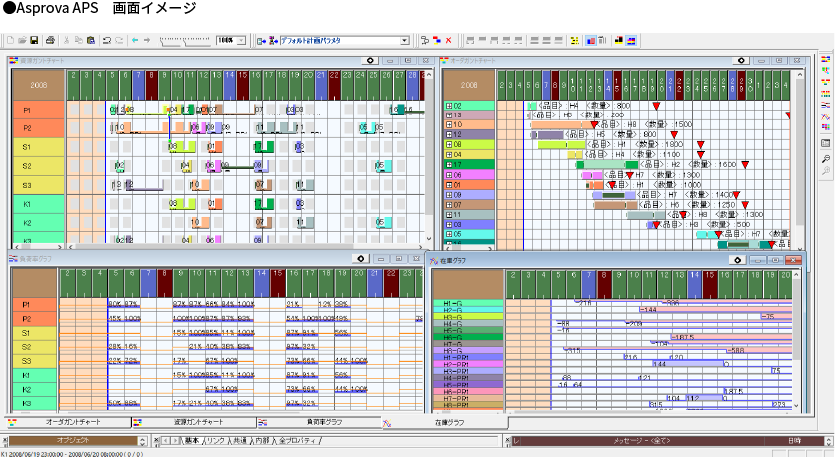
Product Features
- 1) Equipped as standard with heuristic functions for planners to consider
-
- Finite capacity allocation constraints
- In-process inventory Min plan
- Backward allocation + return forward allocation
- Push backward allocation
- Specification summary
- Batch annealing
- No interruption time
- Consideration of constraints in subsequent processes
- Consideration of worker constraints through sub-resource registration
- Order split/work split
- Multiple master settings for items
- Multiple resource allocation constraints
- Inventory expiration constraints
- 2) Coordination by multiple planners
-
- Coordination by individuals in charge of planning each process
- 3) MRP deployment
-
- Inventory information and automatic replenishment settings enable MRP deployment according to sequence planning.
Benefits
- Reduce planning time
- Simple scheduling of complex and individualized production load plans and input sequence plans that span multiple processes allows for quick adjustments.
- Guaranteed delivery date for rush orders
- By taking in and scheduling express orders, it is possible to provide highly accurate delivery dates that take into account production constraints.
- Effective use of bottleneck resources
- Maximize throughput by effectively utilizing bottleneck resources while considering constraints
- Achieving minimization of in-process inventory
- In-process inventory can be suppressed by taking into account the conditions of effective resource utilization (Capacity leveling) and delivery date adherence, which are contradictory to the minimum inventory condition.
- KPI to evaluate multiple scenarios
- Evaluate each scenario with KPIs preset for multiple planning scenarios to help speed up decision-making
- Achieving speedy response to changing circumstances
- Even if the planning method changes due to changes in business conditions, Asprova APS is highly versatile and can reflect changes in requirements without the need for development. This enables early response to requirements changes and decision-making without delay.
Features of B-EN-G’s Asprova APS Implementation Support
- Standard process construction support
- Planning work is a thought-process type of work in which one person gathers information, organizes information, analyzes information, and makes decisions on an Excel spreadsheet. If the current way of doing things is systematized as it is, it will become an individualized scheduling system. At B-EN-G, our consultants are well versed in the characteristics of this type of planning work and will start by supporting you in improving your business.
- Requirement definition using a real model
- It is said that scheduling systems are difficult to extract all requirements without missing anything. At B-EN-G, we create a real model in about a month that incorporates the master data (Generally all cases) and planning data (Planning period) used in actual work into the prototype created through simple interviews. We proceed with the requirement study in a simulated operational test-like manner to prevent requirement omissions.
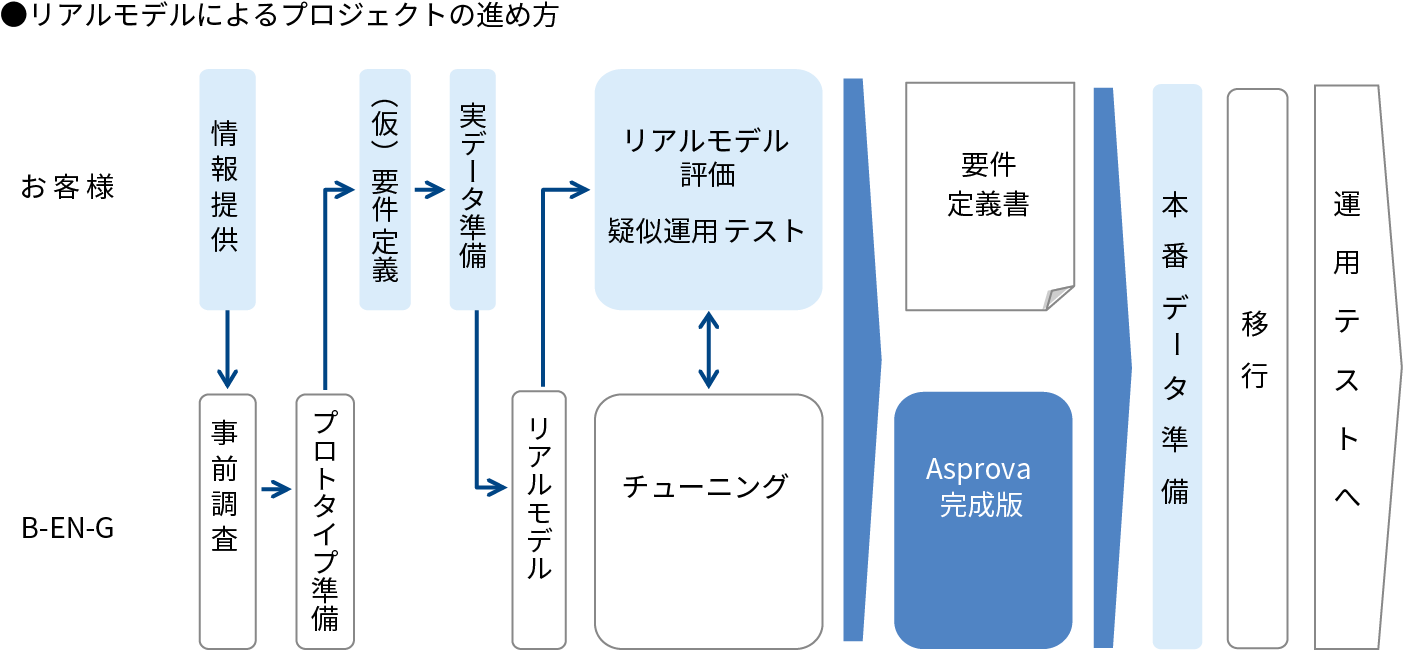
Related Pages
Click here for the special page for process industries such as pharmaceutical manufacturing.