Speaker: Business Engineering Corporation
Masanari Gyoji, General Manager of Product Development Division 3, Product Development Department, Product Business Division
Since 1998, he has been working at Toyo Engineering Corporation, where he is involved in electrical design work for chemical plant construction.
In 2000, he transferred to Business Engineering Corporation, where he was in charge of planning, development, promotion, and implementation of the company's in-house developed software for the manufacturing industry, the mcframe series. He is a certified small and medium-sized enterprise management consultant and MOT (Master of Technology Management).
In recent years, awareness of CO2 reduction has increased in Japan, and an increasing number of companies are aiming to improve their corporate value by incorporating environmental measures into their management strategies. Some companies, particularly large ones, have even gone so far as to disclose their supply chain emissions.
In some industries, pressure is growing on business partners to calculate their carbon footprint (CFP), and this will likely become a significant burden for many companies in the future. In this context, Business Engineering Corporation (B-EN-G), which developed its own production management package "mcframe" and has introduced it to over 1,500 manufacturing companies, has developed a CFP calculation system, "mcframe 7 CFP," by utilizing the package's cost management mechanism.
CFP management based on actual conditions to lead to CO2 reduction activities
--Please tell us the reason behind adding the CFP calculation function to the production management system.
As you know, environmental response is becoming a must in the manufacturing industry, and in addition to disclosing CO2 emissions in corporate activities, companies are being required to visualize their environmental impact using CFP, which is the CO2 emissions per product. In particular, companies that supply parts to major automobile manufacturers and major electronics manufacturers and make up the supply chain are being asked to take specific measures, and if they cannot do so, they may be excluded from the business. Pressure is rapidly increasing. However, the reality is that CFP calculations are a heavy burden to perform manually, and it is difficult to secure the resources to do so. Therefore, we thought that the cost management system technology that we have been good at could contribute to solving this problem. As a result, we released mcframe 7 CFP in January 2023 as a new function of the production, sales, and cost management package software "mcframe 7".
Currently, there are various CFP calculation tools, but most of them are calculated based on fixed information at the time of product design. However, in actual production, energy usage varies seasonally, and yields also fluctuate daily. If CFP calculated based on such information is not used, it will be difficult to link it to activities to reduce CO2 emissions. Therefore, we thought that by using the mcframe system, which aggregates performance data from the entire product manufacturing process, we would be able to provide CFP information that is closer to the actual situation.
mcframe 7 CFP can calculate by importing the production results from the production management system, so you can calculate values that reflect the actual situation, taking into account factors such as yield. Calculations can be made in short cycles of one to several months, making it possible to grasp time-series trends such as seasonal fluctuations and reductions due to reduction efforts. Furthermore, emissions can be confirmed from the perspective of each product, component, process, etc., making it possible to find hot spots and consider focused measures. It is also possible to grasp differences from standard values assumed in the design.
It takes time to compare the raw materials, parts, and materials needed to produce a product with publicly available information on basic units, but once you get past that, calculations can be automated if you can set the data in mcframe 7 CFP as master data. That is the simple benefit of using mcframe 7 CFP.
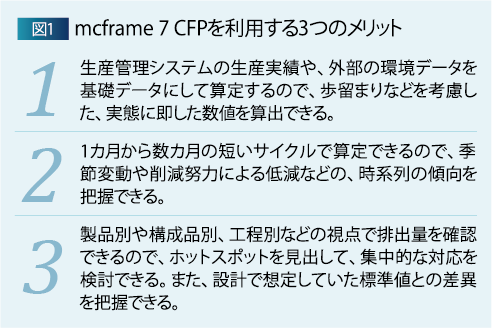
-- Please tell us about the similarities between cost accounting and the system for calculating CFP.
CFP calculations are based on the cost management function of mcframe. Costs are calculated by accumulating raw material costs, allocating electricity charges used in the assembly and manufacturing process, and combining these costs. CFP calculations are based on the same concept, and can be calculated by combining the allocation of CO2 emitted during the procurement of raw materials and parts and the CO2 emissions associated with energy consumption such as electricity.
Figure 2 uses ballpoint pen manufacturing as an example. The raw material cost per ballpoint pen can be calculated as 35 yen by simply adding up the raw material costs of each component. Furthermore, the electricity cost for the assembly process is allocated to the assembly process. Here, the calculation is made such that "100 yen out of the total electricity cost of 10,000 yen is spent on this assembly process," in other words, "electricity cost = 0.1 yen," and allocation is made. The sum of these values is the total cost of 35.1 yen. CFP can be calculated by replacing this with the amount of CO2 emissions.
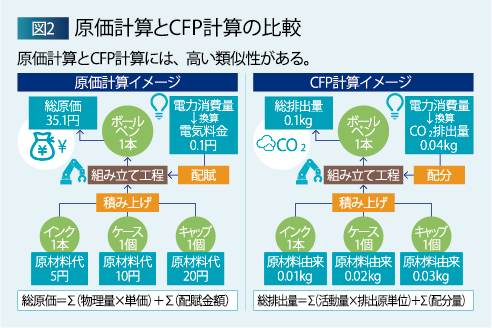
Taking the lead in CFP calculations with the aim of becoming a company of choice in the market
--Please tell us about the reaction since the release of mcframe 7 CFP.
Although the level of interest varies depending on the field and the size of the company, many customers are showing interest in this. Many inquiries were from companies that felt it was essential to start working on this issue, as the quantity and quality of CFP presentations requested by business partners was increasing year by year. Despite pressure from the market and customers, some companies have taken an aggressive stance, saying, "By grasping and visualizing the actual CFP value, we can appeal to the market that we are proactively working on CO2 reduction activities ahead of others, and become a company chosen by the market," and these companies are actually working on PoC (Proof of Concept).
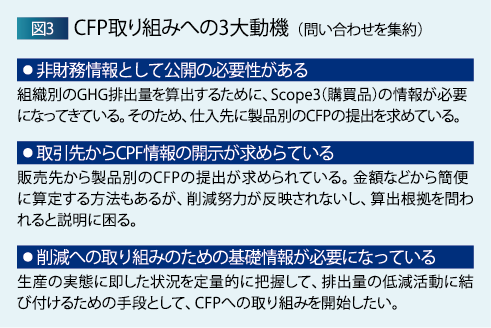
Another important commonality between cost and CFP is how they are used. Cost can be used for cost reduction activities at the company's design and manufacturing sites, and for financial accounting purposes such as reporting to outside parties such as shareholders and investors, and the same is true for CFP. mcframe 7 CFP is intended to be used primarily at the company's design and manufacturing sites. In other words, it is a system for the PDCA cycle of environmentally conscious manufacturing, which involves "setting standards, tallying up results, understanding the difference between the two, and making improvements."
To explain in a little more detail, in cost management in the manufacturing industry, it is important to compare the estimated cost at the upstream design stage with the cost calculated from the actual results after the assembly and manufacturing process, understand the difference, and then proceed with improvement activities for hot spots where labor hours and costs are being consumed. mcframe 7 supports the implementation of this PDCA cycle for cost management on-site. Similarly, in CFP calculation, by linking with the production management system, it is possible to calculate CFP based on the actual results of the manufacturing site, and to implement the PDCA cycle by determining how the actual results were compared to the target CFP and what measures can be taken in the future. We believe that when manufacturing industries realize environmental management, a CFP calculation system that reflects such production results is necessary.
--I understand that one customer has already completed the CFP calculation PoC in December 2023. What kind of feedback have you received?
The customer who carried out the PoC manufactures parts used in computers, office equipment, audio-visual equipment, home appliances, automobiles, aircraft, buildings, etc. Although the number of items is very large at 20,000, this time we narrowed it down to 13 major products and carried out the PoC for about four months. After the PoC was completed, the person in charge commented, "I'm glad we carried it out. We were able to clarify the organizational and technical issues for expanding CFP calculation to all products." Although the electronic parts industry to which the company belongs has a history of CFP initiatives, they have not yet fully adopted it, so the company must find the right answer by itself. The results of the PoC were that they were able to uncover and organize issues in four areas: "methods for investigating and collecting basic data," "creating a cross-departmental system," "policy for using the calculation results," and "functions of the calculation system, mcframe 7 CFP." Based on the results of this project, the company plans to continue efforts to resolve the issues and consider expanding it to all products.
Creating a cross-departmental system requires cooperation from, for example, the general affairs department, which keeps track of electricity consumption, charges, and waste information, the design department, which manages information on materials and outsourced parts, and the purchasing department, which handles material procurement including packaging materials. Another important outcome of the PoC at the company was the creation of a common understanding that "each business department should take a strong sense of responsibility in working to reduce CO2 emissions and calculate CFP."
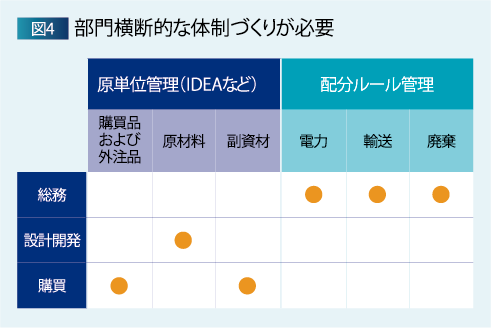
We want to provide an environment where CFP can be managed from design to manufacturing.
--What are you aiming for with the mcframe family based on the theme of CFP? Please tell us about your future developments.
First, regarding CFP calculation, we will continue to enhance the functions of mcframe 7 CFP in response to market needs and requests from customers who have implemented PoC. In addition, we plan to make it possible to visualize CFP on the BI tool "mcframe COCKPIT" so that customers can use the results of CFP calculation as a management indicator. Furthermore, we are planning to integrate CFP and cost information to evaluate the balance between environmental friendliness and economic efficiency. In addition, in order to realize a system that allows environmental impact consideration when selecting materials at the design stage, we are considering linking with PLM "mcframe PLM", which manages design data such as BOM, and plan to start discussions with Zuken Presite, the developer. If linking with PLM is realized, it will also be possible to link with Zuken's PDM "DS-2" and board design CAD "CR-8000 Design Force" in the future. Like cost, it is said that "80% of the product life cycle of CFP is decided at the design stage," so we would like to cooperate with Zuken and Business Engineering to create an environment where customers can incorporate information from the design stage and performance data, and make better products while running the PDCA cycle.
*This article has been re-edited from an article published in the 32nd issue of "from Z," a customer information magazine from Zuken Co., Ltd. To see the full article in the 32nd issue of "from Z," please click here.