Speaker: Business Engineering Corporation
New Product Development Headquarters
Marketing Planning Division, Product Planning Department 1
Toshio Fukasawa
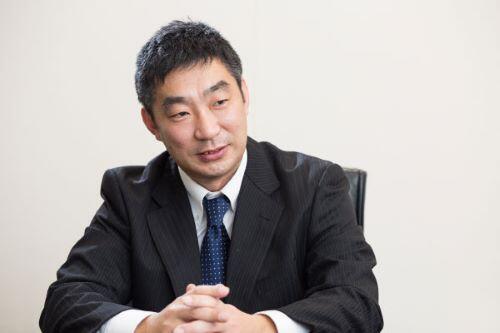
Although the manufacturing industry is moving towards digitalization, the reality is that there is still a lack of data that contributes to work improvements and productivity enhancements. In particular, the preparation of data on "workers" has not progressed, making detailed analysis and work improvements difficult.
Toshio Fukasawa of the Product Planning Division 2 of the New Product Development Headquarters' Marketing Planning Department is very concerned about this issue, and has developed a prototype that embodies his ideas. By conducting PoCs (proof of concept) together with companies that actually have issues, he is working to refine a solution that will enable the capture and analysis of data on worker movements and posture.
The "Man" area is a data "dead spot"
It is said that productivity in the manufacturing industry can be improved by allocating management resources in a balanced manner to the so-called "4Ms" of "Man (workers), Machine (equipment), Material (raw materials), and Method (work methods)."
What is required to make such accurate judgments is data (numbers) that have been indexed with objective evidence. For "Machine" and "Material" of the above 4Ms, data collection and indexing have been achieved to a considerable degree through systems such as ERP (Enterprise Resource Planning), MRP (Material Requirements Planning), MES (Manufacturing Execution System), and SCM (Supply Chain Management). For "Machine", although there has been some delay, the approach of IoT (Internet of Things) is making progress in collecting and visualizing data that was not possible before, and linking with peripheral systems.
However, there is one area that remains almost untouched. Since joining the company in 2000, Fukazawa has been involved in consulting on the implementation of ERP-based core systems and the development and integration of MES for many manufacturing companies, and is currently working as a data scientist. He sees the "Man" area as a data "dead spot."
Fukasawa points out the problem, "No matter how much you optimize machinery and work methods, if the workers cannot adapt, the efficiency of the factory as a whole will not be achieved. In addition, there is a global trend of strict scrutiny of safety at manufacturing sites, and there is an urgent need to create a system that can objectively evaluate the physical strain caused by work in numerical terms."
Of course, even in today's production processes, there is still data on workers. However, all that is collected is "result data" such as the time a worker spends on a process and the number of defective products produced, and the evaluation of the body movements and postures that are the underlying causes is almost unknown. For example, in the field of sports, research on forms for efficiently using the muscles of the whole body according to each sport has progressed considerably, but the reality is that analysis of worker movements in the manufacturing field is lagging behind.
Fukasawa emphasizes, "That's why I thought it would be worthwhile for me to take the lead and try this. Since labor shortages due to the aging population are becoming serious issues in manufacturing, this will also be of great social significance."
Bring the prototype to the manufacturing site and start PoC
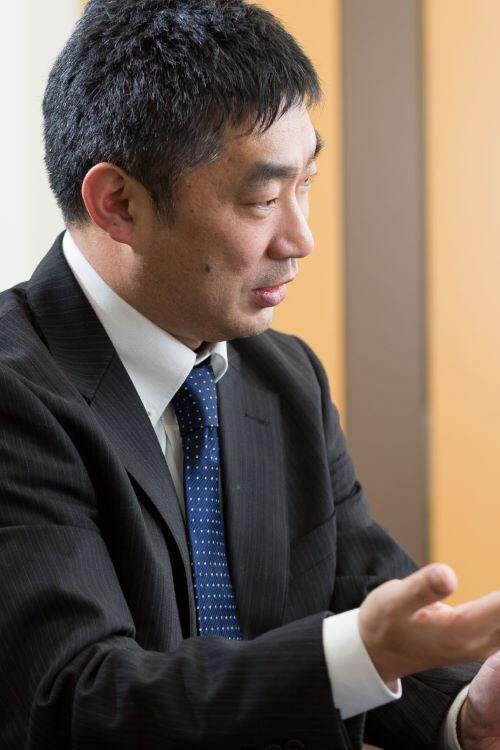
In this way, Fukazawa created a prototype system that converts worker movements and postures captured by motion sensors and cameras into 3D data and visualizes them.
However, personal ideas can only go so far. Whether this system will be truly useful or not will not be clear until it is deployed in an actual manufacturing environment.
"For one thing, it's not even clear how much need there is for digitizing worker movements and postures in actual manufacturing sites. Even if people see value in digitizing worker movements and postures, they won't be able to put it into practice unless they can look at it and determine what is good and what is bad. In any case, we can't move forward unless we understand the true nature of the issues our customers are facing," says Fukasawa.
Fukazawa then searched for a company to embark on a PoC with him, and found an automobile manufacturing company that showed strong sympathy.
"The customer had long felt that in order to ensure worker safety and improve productivity, it was necessary to verify things like movements and postures at the manufacturing site. However, they didn't know how to achieve this, so they were thinking of recording and monitoring on video. When we presented our prototype to them, they gave it high praise, saying, 'With this system, we can obtain much more multifaceted and accurate data than the method we were trying to use, and we can easily link this to subsequent analysis.'" (Fukazawa)
We are still only halfway to solving the problem of overall optimization
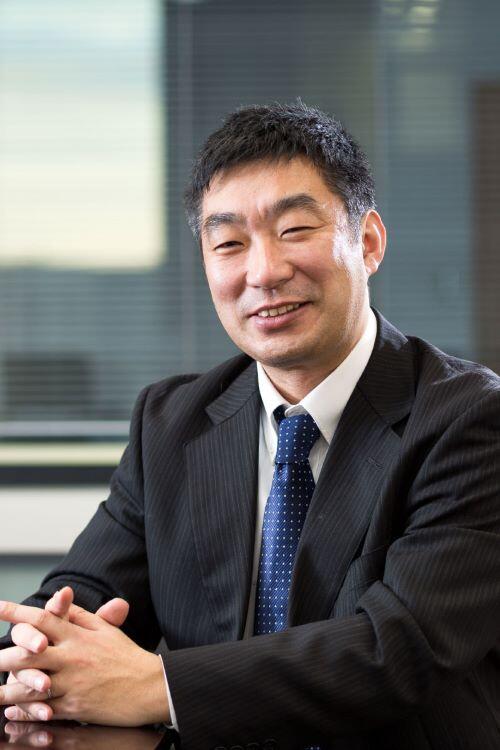
What results did the company and Fukazawa achieve through the PoC? First, from the perspective of ensuring worker safety, there was 3D model analysis, which quantitatively evaluates posture and movement from the distance and angle between skeletal points of the body. "We evaluate postures that put strain on the lower back, shoulders, wrists, etc. for each process, and any data that exceeds the standards is judged as a risk. We also evaluate the work time and degree of strain, and work to improve the work," says Fukazawa.
Furthermore, from the perspective of work assurance, such as compliance with work procedures, identification of abnormal behavior, and error prevention, movement line analysis, which quantitatively and visually grasps movement lines by measuring distances of hands and feet and 3D trajectories, has been extremely effective. "We can quantitatively grasp the difference from the standard based on indicators such as the time, number of times, and distance when moving to work locations and tool and parts storage areas, and detect abnormal behavior and identify areas for improvement," says Fukazawa.
The current "mcframe MOTION" is a product that was developed by generalizing the main parts of the functions that brought about the results described above and implementing them in a system.
However, Fukazawa himself believes that efforts to digitize workers' movements and postures are "still only halfway there." Currently, data acquisition and analysis within the closed scope of man has finally made headway. Even if "good movements and postures" are identified as a result, whether this leads to true improvements in work and productivity is another matter. Only by achieving integrated analysis of data spanning machines, materials, and methods can it become possible to solve problems with overall optimization.
Even in the manufacturing industry, the products and business formats involved are diverse, and the data required varies greatly depending on the business, objectives, and challenges of each company. Therefore, Fukazawa, who says "there is a mountain of work to do," has a continuing challenge ahead of him.
"Manufacturing customers are cautious about everything, so no matter how innovative an idea you present, they won't take action if it's nothing more than armchair theory. Once they see the actual product and are able to evaluate it, they will take it seriously and begin full-scale discussions. In short, the most important point is how I can give the customer awareness and encourage a chain of ideas through the various elemental technologies I present to them." (Fukazawa)
Although digitalization in the manufacturing industry appears to be progressing, there are still many areas where it has not yet been implemented. This is why a down-to-earth approach is required. As a data scientist who leads data-driven problem solving while closely monitoring the evolution of hardware and software technology, Fukazawa plans to realize things that have not been possible or that were never even thought of before at many manufacturing sites.