Speaker: Business Engineering Corporation
Solution Business Headquarters
SCM Solutions Division 1, SCM Solutions Department 1
Satoshi Yanuma
Maximize throughput in your production plant
Supporting the renewal of scheduling operations in response to increased production capacity
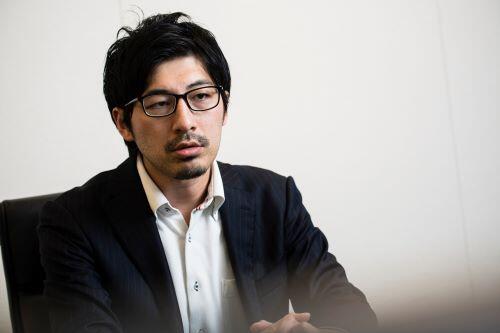
Within the manufacturing industry, the design and systemization of planning operations in the process industry in particular requires advanced know-how and experience.
This will be a case study of the efforts the consulting team, including Satoshi Yanaginuma of the SCM Solutions Division 1 of the Solutions Business Headquarters, has been making at a certain steel company to revamp its planning operations model and build a system to implement it.
Understand changing situations in real time
Flexible schedule changes are required
The pig iron produced in the blast furnace goes through a steelmaking process to remove impurities and becomes pieces of steel called slabs or billets. These pieces of steel are then processed in various types of rolling mills to become products such as heavy steel plates, hot-rolled steel plates, cold-rolled steel plates, and high-performance thin steel plates.
The team at SCM Solutions Division 1 of the Solutions Business Headquarters, to which Yanaginuma belongs, was requested by a steel company to undertake a consulting project to build a planning operations model for one particular step in the steelmaking process.
This process involves post-processing, in which materials are processed according to complex input order constraints, and pre-processing, in which the material conditions differ for each input material. The steel company wanted to improve the throughput of the entire plant by increasing the production capacity of the pre-processing, which was a production bottleneck. To achieve this, they had to re-examine the basic principles of planning operations and at the same time reconstruct the IT system (scheduler) that would reliably execute those plans. However, this was no easy task.
"Until now, pre-processing was a bottleneck, so we always had work-in-process inventory before this process, but with the increase in pre-processing capacity, there is no longer any need to have work-in-process inventory, and the critical path will shift to post-processing, which is continuous processing. In order to eliminate work-in-process inventory before this process, we need to synchronize pre-processing, whose processing time changes depending on the condition of the materials input, with post-processing, which has complex input order constraints."
"Furthermore, if the upstream process that manufactures the materials is unable to manufacture the materials to the planned specifications, the replacement materials will have to be input from the work-in-process inventory. We must find materials from the work-in-process inventory that meet the complex input sequence constraints of the post-processing and can be processed in the shortest possible time for the pre-processing, and instantly calculate the optimal input sequence by combining them with the materials that are input directly from the upstream process. We must grasp this changing situation in real time and quickly reconstruct a schedule that optimizes the entire process."
Algorithms and systems that respond to changing bottlenecks
Build

To solve the problems described above, Yanaginuma and his team first tackled the task of developing a scheduling algorithm that would maximize the production efficiency of post-processing in continuous processing within a process.
"The ability to connect post-processing without delay directly impacts throughput throughout the entire factory. However, pre-processing requires a large amount of energy, so it is an indicator that cannot be ignored from the perspective of manufacturing costs. We therefore considered an algorithm that would prevent a drop in production efficiency as much as possible. The algorithm was designed based on the Theory of Constraints, which B-EN-G consultants had implemented in past projects.
Furthermore, in order to establish such a major shift in basic scheduling policies at the production site, it is essential to change the way planners think, so we also focused on defining KPIs with an eye to future operations."
The next step was to build a system that would execute the newly developed algorithm. "To execute the created schedule, we had to clear a wide range of constraints, such as special manufacturing specifications, restrictions on equipment use, and priority processes. We had to organize documents and manufacturing manuals scattered around the factory, and
We gathered all the information and interviewed the relevant parties, organizing it one by one down to the level of the system specification form of constraints that B-EN-G has, and then modeled it.
We implemented the hundreds of constraints that were identified in this way into the system. We also implemented them separately as hard constraints and soft constraints (rules). Basically, automatic scheduling is based on hard constraints, but it also supports optimal production by issuing alerts for violations of soft constraints."
Furthermore, to ensure the performance required to synchronize processes in the shortest possible time and quickly rearrange the schedule while capturing changes in the situation in real time, the new system employs an in-memory database and adopts a push-type data exchange method from the host computer, which is responsible for collecting performance data.
"The background to the creation of this system was largely due to B-EN-G's extensive know-how in data management in the manufacturing field. By utilizing experience and knowledge on how to process and normalize performance data to achieve efficient scheduling and how long that processing would take, we were able to build a system that performs rescheduling at two-minute intervals based on real-time performance information collected from equipment, rather than batch-based performance collection and rescheduling."
Reflecting ideas derived from projects in company-wide methodology
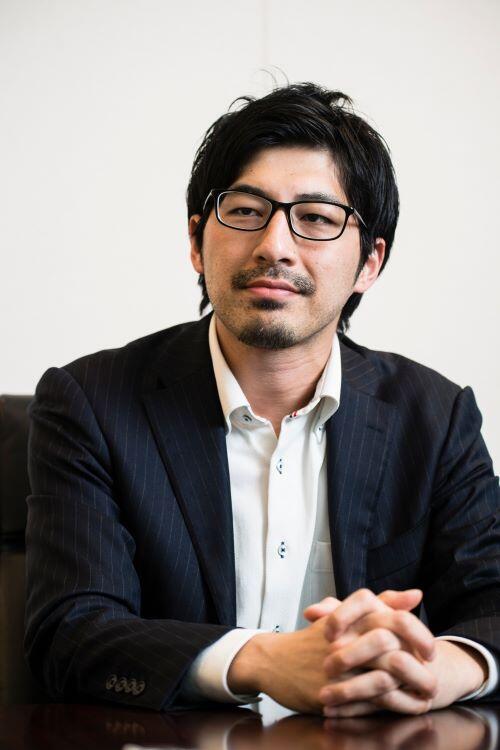
Yanaguma lists the following three points as important when consulting on planning operations and systems such as this one:
The first step is to define the planning work model. By dividing elements such as target equipment, algorithms, constraints, and screen operations, and defining the target level for each, it is possible to materialize the planning work that the customer is aiming for (further improving throughput, allocating resources more efficiently and fairly between processes). "It is important to consider and present planning work models to our customers before they do. We are always looking to use this as an opportunity for our customers to materialize their own ideas."
The second is to have a perspective of continuous improvement. Planning work requires continuous improvement through daily operations, so goals also need to be reviewed accordingly. "In order to set and evaluate new goals, it is necessary to refine the PDCA (Define Goal, Do It, Evaluate, Define the Next Step) cycle for each element of the planning work model mentioned above. Also, in order to continue making continuous improvements, it is important for customers to have improvement specialists in both their user departments and their systems departments."
Third, consider the overall design of the system
In planning work, it is important to have an optimal system configuration to run the PDCA cycle.
"In addition to automating scheduling through the system, you need to design the entire system configuration, taking into account factors such as how to collect performance data from systems like ERP and MES, how to cleanse it to match the plan, and then link it together. You also need to consider how to evaluate the plan (comparing it with past plans and performance, displaying it in multiple dimensions, etc.) and how to adjust the plan (how smoothly you can adjust the plan after evaluation).
In addition, planning work has layers such as "S&OP → supply and demand → production → scheduling," and the constraints and rules that need to be taken into account differ for each layer. It is necessary to find the right balance by considering the client's current work, existing systems, business goals, etc."
One of B-EN-G's strengths is its ability to generalize the above-mentioned ideas and accumulate them as know-how within departments and across the organization in order to ensure a high QCD for its customers' business issues. In other words, it is able to "engineer business."
[The contents are current as of September 2017]