Speaker: Business Engineering Corporation
Solution Business Headquarters
SCM Solutions Division 2, SCM Solutions Department 4
Project manager
Yu Ohtake
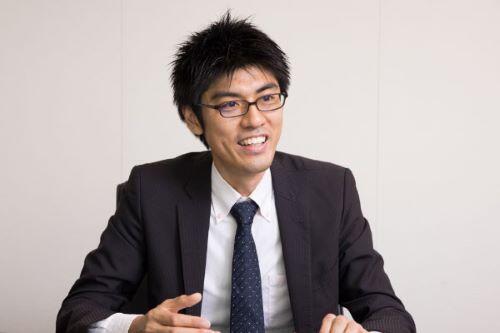
In recent years, the pharmaceutical industry has been facing increasingly strict regulations and complex responses in order to address the rapid increase in products produced in developing countries due to the globalization of pharmaceutical manufacturing plants and the growing number of deficiencies in quality systems.
In this process-focused environment, B-EN-G is demonstrating leadership based on its extensive track record and experience in solving problems faced by pharmaceutical companies, which require particularly strict data handling. The consulting team to which Otake Yu belongs, from the SCM Solutions Division 3 of the SCM Solutions Division 2 of the Solutions Business Headquarters,
We will introduce the projects they are working on and explore why pharmaceutical and medical companies see B-EN-G as a "base for business innovation."
Achieving "ERP-MES integration" that leads the IoT era
Currently, the SCM Solutions Division 3 of the SCM Solutions 2nd Division of the Solutions Business Headquarters provides consistent support to a major pharmaceutical company, from construction to maintenance of an integrated SAP ERP and MES system, and has 20 to 40 members on-site.
Recently, IoT initiatives in the manufacturing industry have been attracting attention, as symbolized by the keyword "Industry 4.0 (Fourth Industrial Revolution)." In fact, the vertical integration project between ERP and MES that has been underway in the pharmaceutical industry since the early 2000s can be said to be a precursor to this trend.
Yu Otake, who joined the company in February 2010 and served as maintenance project manager in 2014, describes the features of this ERP-MES integrated system as follows:
"We have achieved integration between the MES and peripheral systems, such as the Supervisory Control And Data Acquisition (SCADA), which monitors the status and collects data from the wide variety of manufacturing equipment dispersed throughout pharmaceutical factories, and the Material Handling System (MHS), which controls automated transport, including in the warehouse. This allows manufacturing workers to operate manufacturing equipment exactly as instructed, simply by following the instructions on the MES screen."
Audit trail recording is essential for pharmaceutical factories
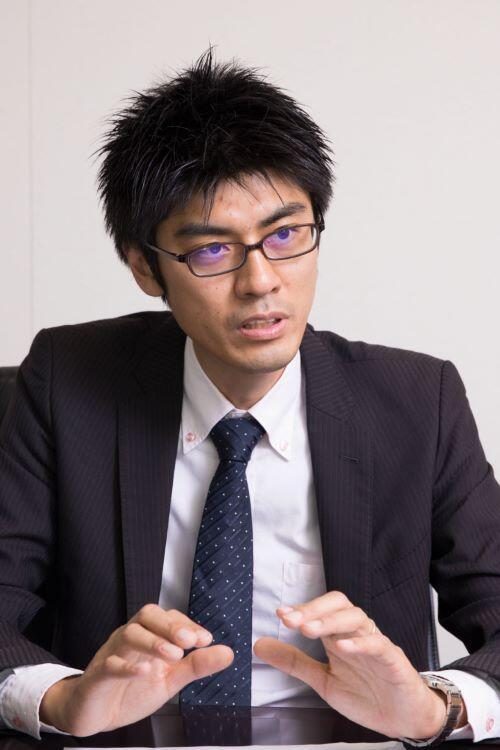
The vertical integration of ERP and MES can dramatically improve productivity in pharmaceutical factories, but there is actually a more important theme than that: compliance. Because pharmaceuticals have an impact on human life, it is legally required to keep all evidence of manufacturing and guarantee that there are no problems with the quality of pharmaceuticals.
First of all, the maintenance of "operation logs" is essential. "What operations did the manufacturing workers perform on the MES screen? For example, if they entered the command 'run the mixer for one minute,' that operation must be recorded accurately. What is particularly difficult is how to deal with irregular events. Even if each piece of manufacturing equipment is operated manually without going through the MES, the details of the operation must be recorded without fail."
Furthermore, these operation logs must be recognized as future "audit trails." To prevent information leaks to unauthorized parties or tampering, they must be securely stored in a system that meets electronic record and electronic signature requirements, such as confidentiality, integrity, and availability.
"In this case, we introduced Electronic Batch Recording (EBR), which complies with FDA (U.S. Food and Drug Administration) regulations, 21 CFR Part 11, which is the de facto international standard for pharmaceutical manufacturing, and enabled long-term storage of operation logs and electronic signatures by the person in charge of manufacturing."
System renewal to strengthen DI (Data Integrity)
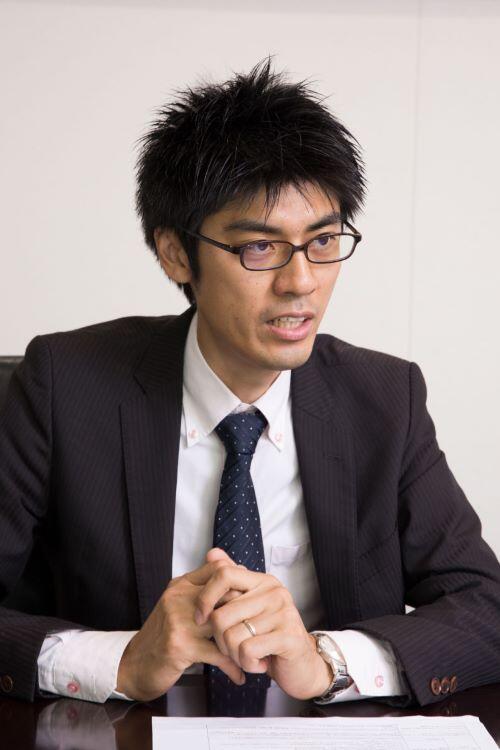
Currently, regulations regarding pharmaceutical manufacturing are becoming increasingly strict on a global level. In response to this trend, Otake has been serving as project manager since August 2016 for the introduction of a system aimed at strengthening DI (Data Integrity). The project began when the support period for the existing SCADA system expired and it became necessary to select and introduce a new package.
1. Attributable: Who acquired and recorded what data, when, from which manufacturing equipment, and the attribution of manufacturing record data
Clarify where responsibility lies.
2. Legible: Improve the readability of manufacturing record data and improve the understanding and proficiency (visualization and understanding) of those involved.
3. Contemporaneous: Realizes simultaneous recording of manufacturing data at the time it is generated (recorded one week after data generation).
etc. are not allowed as they may be suspected of tampering.)
4. Original: Proves that the manufacturing record data is the original and not a copy.
5. Accurate: Ensure the accuracy of manufacturing record data.
B-EN-G has decided to introduce OSI Soft's PI System (※1), a packaged product that meets the above DI requirements and has a proven track record worldwide. Currently, the project team led by Otake is developing an interface with the existing MES as an add-on, and is gradually implementing it.
The background to this is the globalization and internationalization of pharmaceutical manufacturing plants. In particular, in recent years, along with the rapid increase in products produced in developing countries, the increase in deficiencies in GMP and quality systems related to manufacturing has been discovered, and regulatory authorities have issued guidance on the concept of DI, including the correction of these deficiencies. In relation to DI, distribution organizations are also strengthening GDP (Good Distribution Practice), which requires strict management and traceability of product information, and temperature control is becoming stricter with the increase in bioproducts, as well as measures against counterfeit drugs, which are particularly problematic in Europe and the United States. In this situation, compliance measures, including strengthening DI, are the top priority when implementing a system, so it is important to collect information and conduct research on the latest solutions. B-EN-G's ability to deeply understand the changes in the environment and requirements surrounding the pharmaceutical industry and to propose functions that must be implemented in advance is highly regarded by customers.
"B-EN-G has consistently supported a wide range of pharmaceutical operations, from the implementation to maintenance of ERP, MES, and MHS, and has cultivated a long track record and specialized knowledge. This is why we can present optimal solutions that take into account the entire pharmaceutical supply chain."
B-EN-G aims to continue making a definite contribution to improving drug safety and further developing the pharmaceutical industry, and Otake says, "Our experience in the pharmaceutical industry, which is cutting-edge and subject to strict regulations regarding data handling, should naturally be applicable to other industries." The strength of B-EN-G, known as "high performance engineering," is its ability to find optimal solutions based on its extensive track record and specialized knowledge.
*1: The PI System is a real-time manufacturing information management system developed by OSIsoft, Inc. It collects and analyzes time-series data such as production results, quality information, and equipment utilization rates from multiple sources across a wide range of business processes, and realizes real-time visualization and sharing.
[The contents are current as of December 2017]