Challenges
- When domestic companies export products, they need to carry out export procedures such as managing product names and tariff codes (HS codes), and in some cases obtaining and managing product of origin determination numbers. In addition, the parties to whom this information is exchanged are diverse. For this reason, many companies that handle trade affairs are troubled by frequent lack of necessary information or misunderstandings, which require a lot of time and effort to confirm. Furthermore, the more diverse the products handled and the countries to which they are exported, the more diverse the business processes become, which makes it difficult to standardize as desired and tends to make work more dependent on individuals.
Toyota Tsusho's Global Parts and Logistics Headquarters mainly exports parts for automobile production, and faced the challenges mentioned above in its export operations.
Implemented Products/Solutions
Background of the initiative
Considering the systematization of export operations against the backdrop of efforts to promote digital transformation and the coming into force of a new economic partnership agreement
The Global Parts and Logistics Division's Global Parts Business Division is mainly responsible for the overall management of the import and export business of automotive parts, as well as the promotion of digital transformation and carbon neutrality (CN) in the area of global parts and logistics business that Toyota Tsusho is developing. It is divided into four sales departments based on export destinations such as Europe, the US, and Asia, as well as Tokyo and Osaka, and has approximately 220 staff members engaged in its work.
As part of export operations, it is necessary to manage information such as the product name and statistical commodity code (HS code) of the exported product. In particular, if the export destination is a country that has an Economic Partnership Agreement (EPA) or Free Trade Agreement (FTA) with Japan, it is necessary to obtain a Certificate of Origin proving that the product originates in Japan and to manage the associated product origin determination number.
Strengthening the cost competitiveness of Japanese products by receiving preferential tariffs from export destination countries is an important mission, but at the same time, the business process for obtaining a Certificate of Origin is complex, and the documents required differ for each agreement.
There were many different people involved, and all kinds of information was exchanged via email and Excel, so no one knew the details or progress of the work. Work efficiency was heavily dependent on the experience of the person in charge, and the work itself was highly personalized. That's why we aimed to break away from the "email back-and-forth and Excel bucket relay" system.
Reasons for product selection
Aiming for rapid systemization, development using no-code tools was chosen
The main target was the business portion related to the EPA agreement, and initially they considered using a package to quickly systematize it. However, they were worried that introducing a package would lead to a large scale of consideration, and that coordination with other departments would be required, making it difficult to proceed, so they decided to proceed with development using no-code. They thought that if they could increase the IT literacy of end users, they would be able to flexibly respond to changes in the environment and further accelerate the promotion of DX.
Aiming for rapid systemization, development using no-code tools was chosen
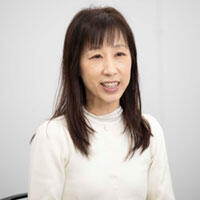
"We told B-EN-G what we wanted to do and what we wanted to achieve, and they made a prototype for us. We told them our requests and questions, and they made a prototype that addressed those needs. When we checked the completed prototype, we found that Business b-ridge had the operations and functions we had imagined. It felt like the idea of 'it would be nice if it could be done like this' had finally taken shape." (Asami Miura, Assistant Manager, Strategy and Planning Group, Global Parts Business Division)
Benefits
Realize visualization of operations, standardization, information sharing, and elimination of dependency on individuals
In a complex business process, communication with many stakeholders was done via email and Excel. "There was a frequent lack of necessary information and misunderstandings, which required a lot of time for confirmation work. In addition, the progress of work was not known to anyone other than the person in charge, and the format for managing information using Excel differed depending on the person in charge, so even other people could not immediately understand it."
"By using the cloud service Business Bridge, we are now able to communicate with all parties involved on a single platform. Also, by making business processes visible, we can quickly find gaps or omissions in work processes, and we can also clarify the required documents, which differ for each trade agreement, and manage them centrally. This has made a significant contribution to eliminating dependency on individuals and improving work efficiency. In an environment in which free trade is expected to expand further in the future, I believe that the EPA system we have created will be a powerful mechanism to support export operations." (Miura)
Future Outlook
Gradually apply no-code development knowledge to other tasks
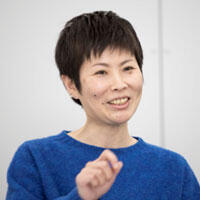
"Because this was our first attempt, we basically had B-EN-G build us a base system, then used it and asked them to add new requirements and make adjustments. After that, we dissected the completed EPA system, learning how it was constructed and how each module worked together. To date, we have used Business Bridge to develop several other business systems. However, the hurdles rise dramatically when we try to get customers to use the system we developed. Our next challenge is how to expand it outside the company." (Izumi Yamada, Group Leader, Strategy and Planning Group, Global Parts Business Division)
"Yamada helped me unravel the EPA system we created with Business Bridge and taught me how to set it up, so I think I've gotten to the point where I can create it to a certain extent on my own. I think it depends on the resources of the user company, but if there are members in the company who are interested in IT, I think no-code development can be expanded more smoothly." (Miura)
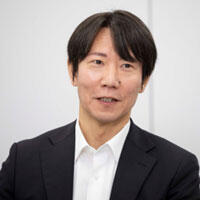
"This time, we adopted no-code development and chose to improve and evolve the system ourselves. However, in cases where specialized skills are required, or for short-term projects with time constraints, or when you want to incorporate the latest technological trends, the cooperation of a reliable IT vendor is essential. In that sense, we hope that B-EN-G will continue to provide us with strong support in the future." (Koichiro Tabe, General Manager of the Global Components Business Division)
Case study company introduction
Company Name | Toyota Tsusho Corporation |
Establishment | July 1, 1948 |
Nagoya head office (head office) location | Nakamura Ward, Nagoya City, Aichi Prefecture |
Business Activities | Domestic trade of various goods, import/export trade, international trade, construction contracting, various insurance agency services, etc. |
Company website | https://www.toyota-tsusho.com/ |
*Please note that organization names, positions, numerical data, etc. in the article are based on the time of the interview and may have changed by current viewing.
Related Solutions
Relevant information and case studies based on solutions presented above.
Related Case Studies
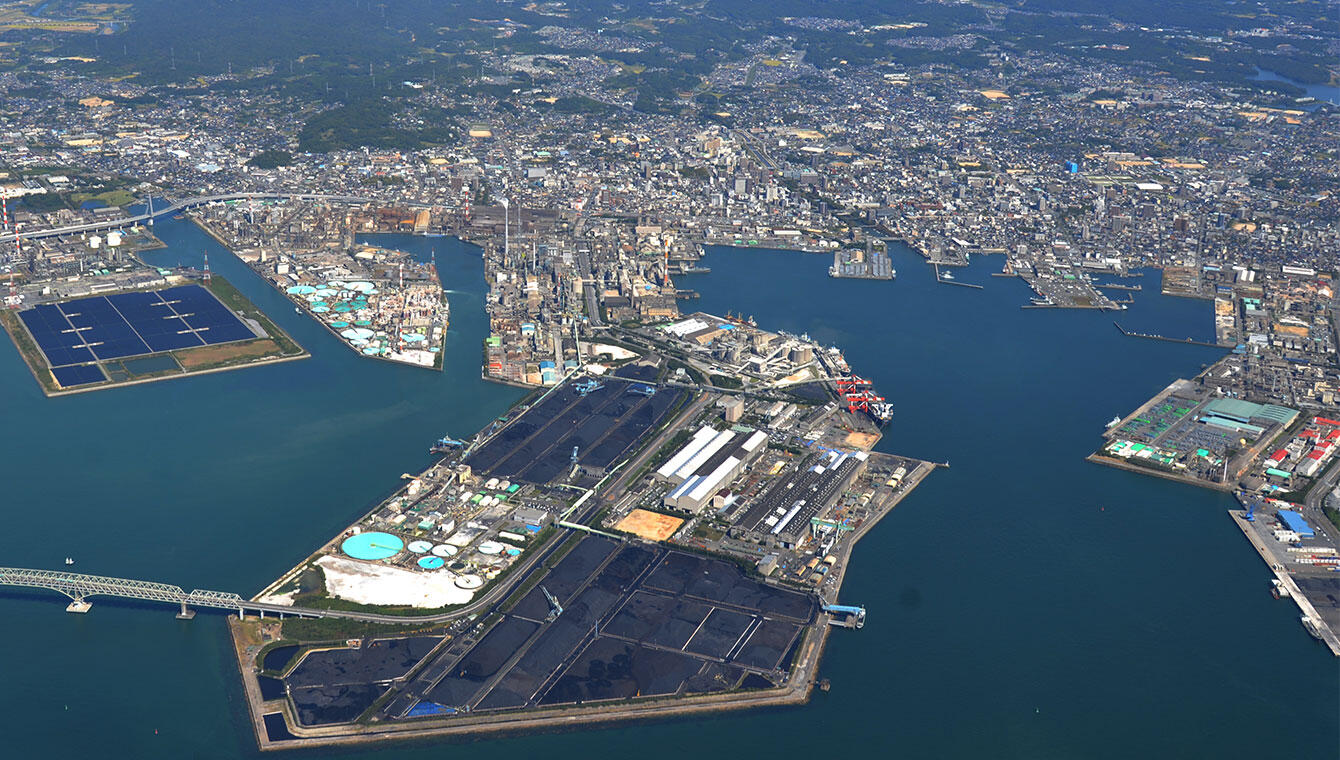
UBE Corporation (Formerly Ube Industries Co., Ltd.)
Improving Productivity and Transforming the Purchasing Process for Indirect Goods Purchasing: Cloud Purchasing Management System "SAP Ariba" Case Study
Chemical
Inter-company collaboration solutions
SAP
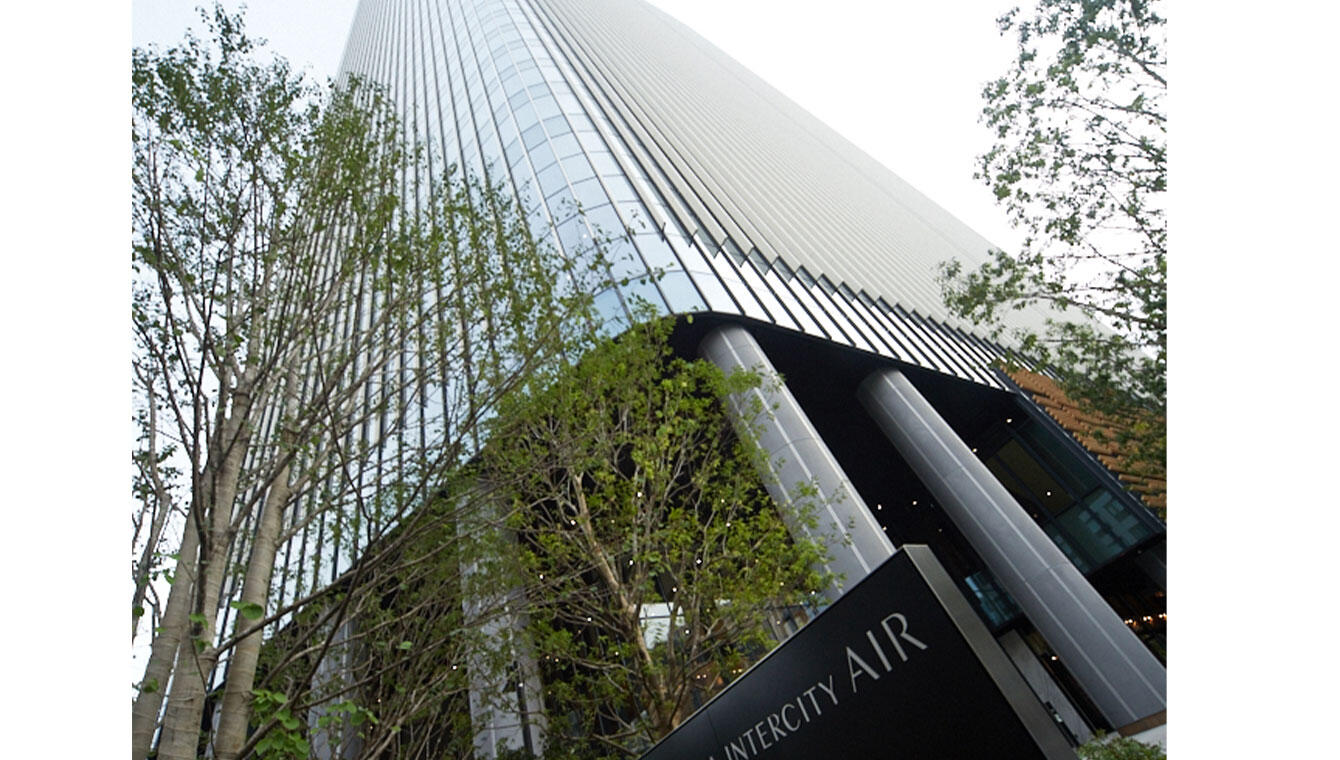
Saison Technology Corporation (formerly Saison Information Systems)
SAP Ariba Case Study: Reforming Work Styles by Enjoying the Benefits of Cloud Services
service
Inter-company collaboration solutions
SAP