Case Study Video
A 4-minute overview of UBE Corporation's story behind the introduction of SAP Ariba, the effects of the introduction, and future initiatives.
View here
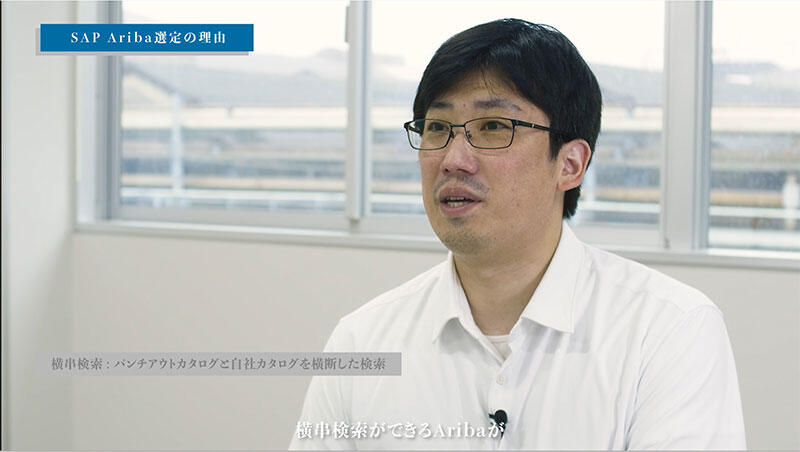
Challenges
- Suppliers have different commercial flows, and prices vary for the same product, which takes time to compare and consider
- Problems caused by connecting various EC sites
- Small companies within the UBE Group where purchasing controls were not effective
Implemented Products/Solutions
Cloud procurement and purchasing management system SAP Ariba
Project Background
Since its founding in 1897, UBE has expanded its business to include machinery, cement, and chemicals, and is active in the global market, inheriting the spirit of "coexistence and co-prosperity" that the company's founder believed united the development of the company and the prosperity of the community. Behind the scenes, the purchasing department has supported this development. The company has been implementing reforms in purchasing indirect goods for many years without severing ties with local suppliers. One of these reforms is the adoption of an online purchasing system to improve the productivity of purchasing operations by reducing the need for one-time quotations.
With the introduction of SAP ERP in 2000, the company introduced an indirect materials procurement system and began placing orders over the Internet. Subsequently, the company increased the number of products available for purchase while linking with a number of BtoB EC sites. However, as the number of products increased, it became difficult to control prices, and connecting various EC sites had its downside.
Hideo Fujimoto, Group 1 Purchasing Department Manager, who has been reforming purchasing operations since 2000, proposed to the developer of the indirect materials procurement system that was being used to improve product search, operability (cross-site search function), and simplify ID management, but the system responded that it would be difficult to implement. He considered other systems, but was unable to find one that satisfied the required specifications, and even if it were possible, the high cost of implementation made it unaffordable.
In 2018, after attending a seminar sponsored by SAP and receiving a presentation on SAP Ariba, they decided to consolidate their procurement functions into SAP Ariba and streamline and optimize their operations, believing that it could provide the functionality they desired.
Reasons for Selecting Solution and B-EN-G
- Unifying the system flow from purchasing to payment
- Cross-site searches are possible, simplifying ID management and speeding up approvals
- Compatibility with core system SAP, considering future upgrade to SAP S/4HANA
When implementing SAP Ariba, the company selected B-EN-G as a partner by comparing the company's experience with SAP Ariba implementation, reliability during proposal presentations, and level of motivation. In addition, the company outsourced the integration with its core system to Ube Information Systems, a group company.
Implementation Project Overview
Target Items
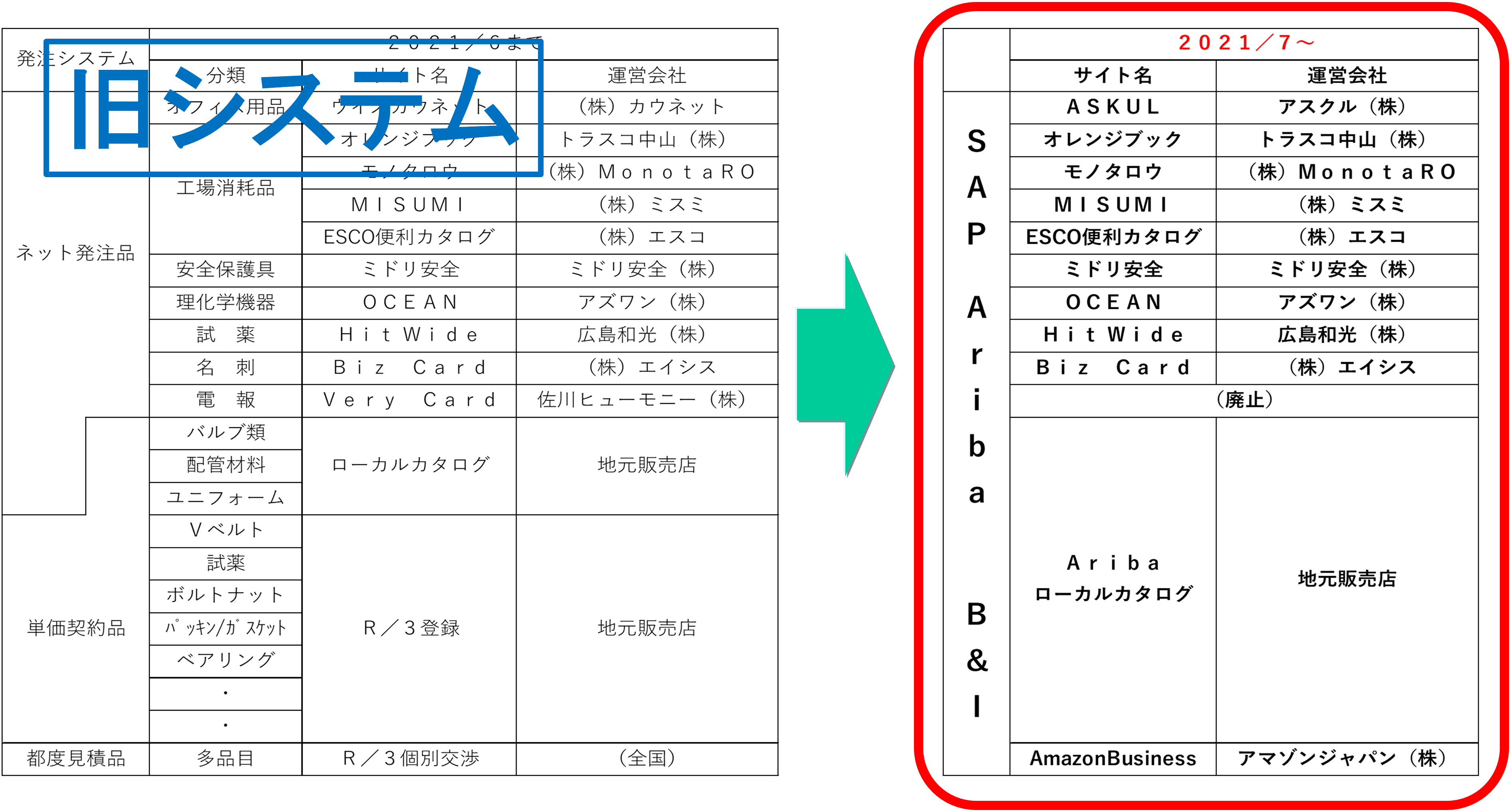
■ Target Items were: (1) Internet orders placed through the existing procurement system, (2) Unit price contracts placed through the core system (SAP ERP) and local distributors as in (1), and (3) Quotations for items that were ordered individually on a case-by-case basis. By introducing Amazon's e-commerce site for corporate customers (Amazon Business), the company aimed to increase the number of merchandise items and reduce the number of quotations, which totaled approximately 60,000 per year.
By consolidating all small-value purchases into SAP Ariba, they eliminated the hassle of logging into multiple systems and improved product searchability without degrading the functionality of existing systems.
"In terms of numerical effects, it is estimated that at least 6,000 hours of work per year would be saved by reducing system changeover time, product search time, and administrative work time, mainly for Net ID applications. Also, the unit purchase cost of both catalog and small-value items is expected to be reduced by several percent," says Mr. Fujimoto.
SAP Ariba also includes its own local catalog purchased from local distributors as described in (2) above. This may be called "coexistence and co-prosperity," but in reality, the items in the local catalog are on more favorable terms than those of other online purchasing suppliers in terms of price, so they will continue to be purchased as is.
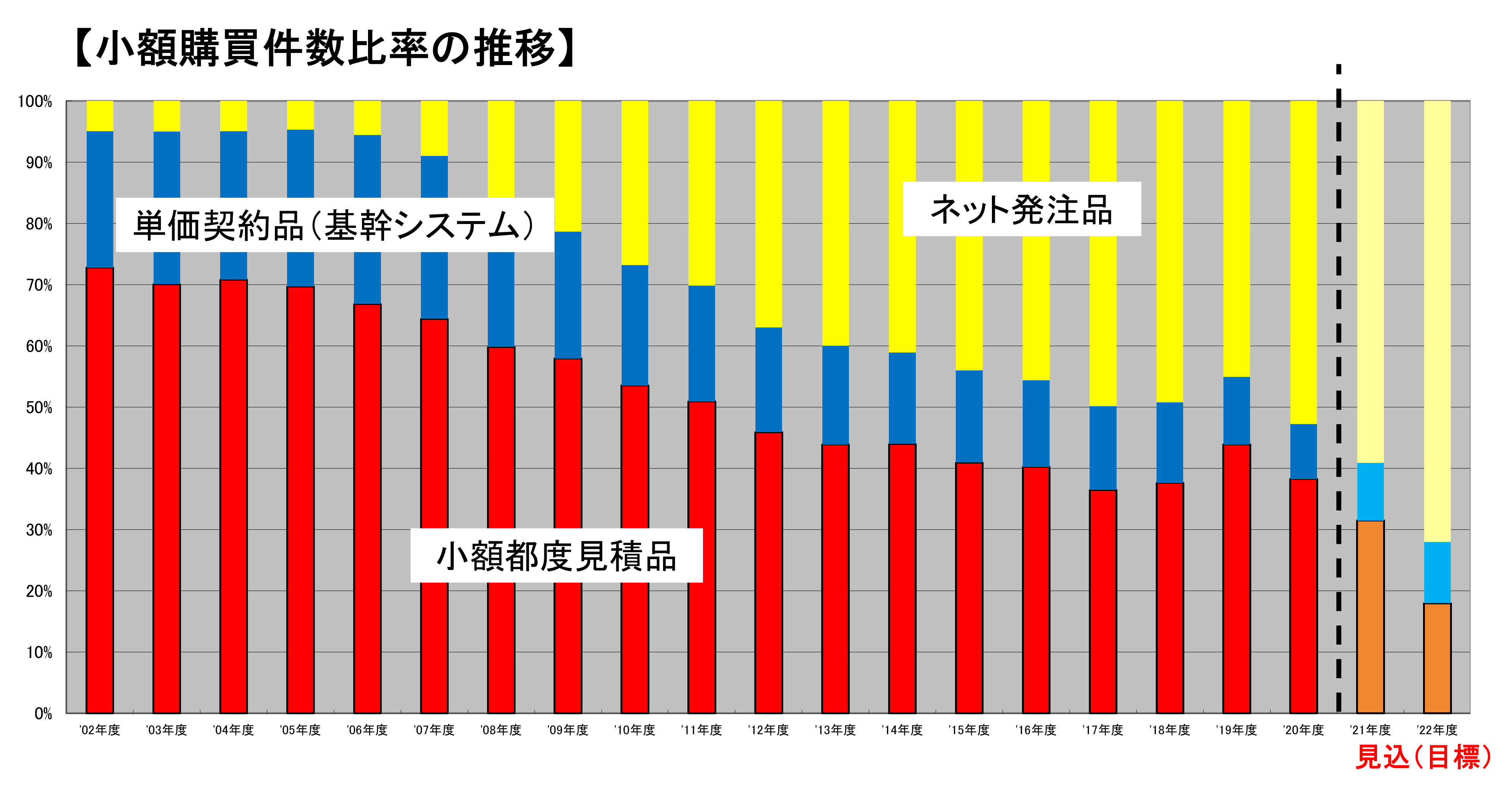
■The reform of indirect goods purchasing that started in 2000 was to increase Internet purchasing (yellow in the graph), thereby reducing the number of small quantity quotations (red in the graph) and the time and effort required to obtain and negotiate quotations and place orders one at a time. Since the start of Internet ordering, the ratio of small quantity quotations has been decreasing year by year, from over 70% in 2002 to less than 40% in 2020, and is expected to be reduced to less than 20% in 2022 through the consolidation to SAP Ariba.
Target Group Companies
Used by approximately 20 group companies (excluding construction materials division, which will be spun off in April 2022)
Mr. Fujimoto said, "In some small companies, the rules for application and approval were paper-based or after-the-fact approvals for purchasing, invoicing, and payment. With the introduction of SAP Ariba, these companies can now incorporate approval workflows into the steps from purchasing to invoicing, and checks and balances can be applied. We believe this is very important from an internal control standpoint for the UBE Group's further development in the future."
Implementation Project Overview
Target Schedule
Complete implementation in 3 months, complete transfer within the company in the first half of 2021, and complete transfer to the target group companies by the end of FY2021.
2019/12~2020/8 Introduction Consideration
2020/11~2021/3 SAP Ariba Implementation, SAP Ariba-core System Collaboration Development
2021/4-6 In-house Production Preparation
2021/7~ Actual Start (Punchout/Local Catalog Purchasing), 8~ Start of Quotation Purchasing
2021/10-12 Group Company Development (approximately 20 companies)
Installation System
Development: 4 persons at Ube Information Systems Co. Purchasing: 5 (including 2 managers)
Key points for Implementation and Operation
Internal Consultation and Budgeting
To persuade upper management, the company clearly stated what it is being introduced for, how effective it will be, and how it will be done.
In particular, since the purchasing department is the department whose mission is to determine how much to lower the cost against the budget, and it is difficult to secure the cost for system implementation, a cost-benefit calculation was performed to clearly express the scope, schedule, and effects of the implementation.
Schedule Management and Division of Roles
The Purchasing Department has an increased workload due to project management in parallel with its normal duties. Therefore, to ensure that the workload is not unevenly distributed among employees, the schedule is thoroughly managed to determine who is responsible for what and when. When issues arise, decisions are made promptly.
Selecting Functions
Maintaining the status quo has no benefits for the transfer. The company will select and discard functions of the existing system, implement business reforms to adapt operations to the standard functions of SAP Ariba, and enhance internal explanations, education, and help desks.
Among the business reforms, there were some critical voices regarding the simplification of the approval workflow and the narrowing down of approvers. Mr. Fujimoto said, "I think most people don't want to do business reform because they have to change their current way of working. Since we have to change that, we need to explain the benefits well," talking about the importance of working with enthusiasm and persistence.
B-EN-G as an Implementation Partner
At the time of selection, B-EN-G was selected from among multiple companies. In fact, Mr. Fujimoto talks about his impressions as an implementation partner as follows.
"I thought they were reliable. They manage delivery dates very well, and they respond quickly to questions we have. Also, when it comes to system implementation, there are cases where other companies say, 'Customers have to choose the features.' However, we were able to receive accurate advice such as "This is the best way to do it," and we were able to move forward calmly as both our company and B-EN-G had decided what to do. I don't think there would have been any problems as I would have been able to implement SAP Ariba if I had followed the guidelines mentioned above. I felt that the methodology was set in stone. The division of roles as to who was in charge of what was clear and it was easy to ask questions. All the members gave detailed explanations, including the points, so it was easy to understand. I think the overall score was about 99."
Expected Effects and Future Plans and Policies
When asked if his evaluation of SAP Ariba has changed between before and after the introduction of the system, Mr. Fujimoto replied, "My expectations for the ability to move to simple business rules have not changed. In addition, as a purchasing manager, I expect to be able to immediately view budgets and product searches, which used to take a lot of man-hours when using multiple online purchasing systems, on a horizontal axis in SAP Ariba, to be able to set approval routes, and to receive shipment data.
Furthermore, "Our company is planning to switch our core system to SAP S/4HANA around 2025. Along with this, we will expand the scope of use of SAP Ariba, including contract work and high-value materials that are currently being estimated on a case-by-case basis. I would like to use SAP Ariba to handle this. Beyond that, we can also consider incorporating raw materials (direct materials), expenses, etc.," he says, expressing his expectations for the future potential of SAP Ariba as the core of company-wide spending.
*SAP Ariba Snap: A program that implements limited SAP Ariba functions in 12 weeks. See B-EN-G's SAP Ariba Snap Service Page
Case study company introduction
Company Name | UBE Corporation UBE Corporation |
Establishment | March 1942 |
Head office location | Minato Ward, Tokyo |
Company website | https://www.ube.com/ube/ |
*Please note that organization names, positions, numerical data, etc. in the article are based on the time of the interview and may have changed by current viewing.
Related Solutions
Relevant information and case studies based on solutions presented above.
Related Case Studies
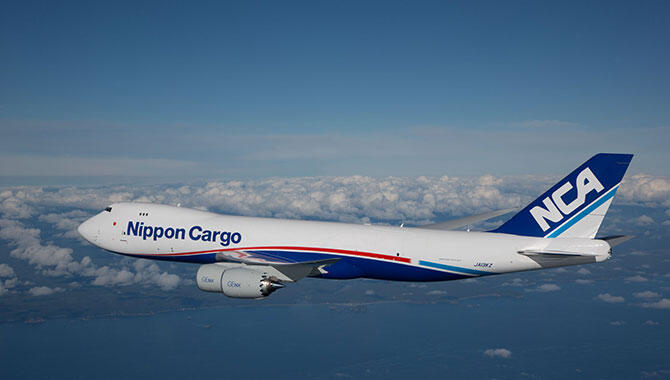
Nippon Cargo Airlines Co., Ltd.
Aiming to Shift to High-Value-Added Businesses: A Case Study of Accounting System Restructuring with RISE with SAP
Logistics
ERP
SAP
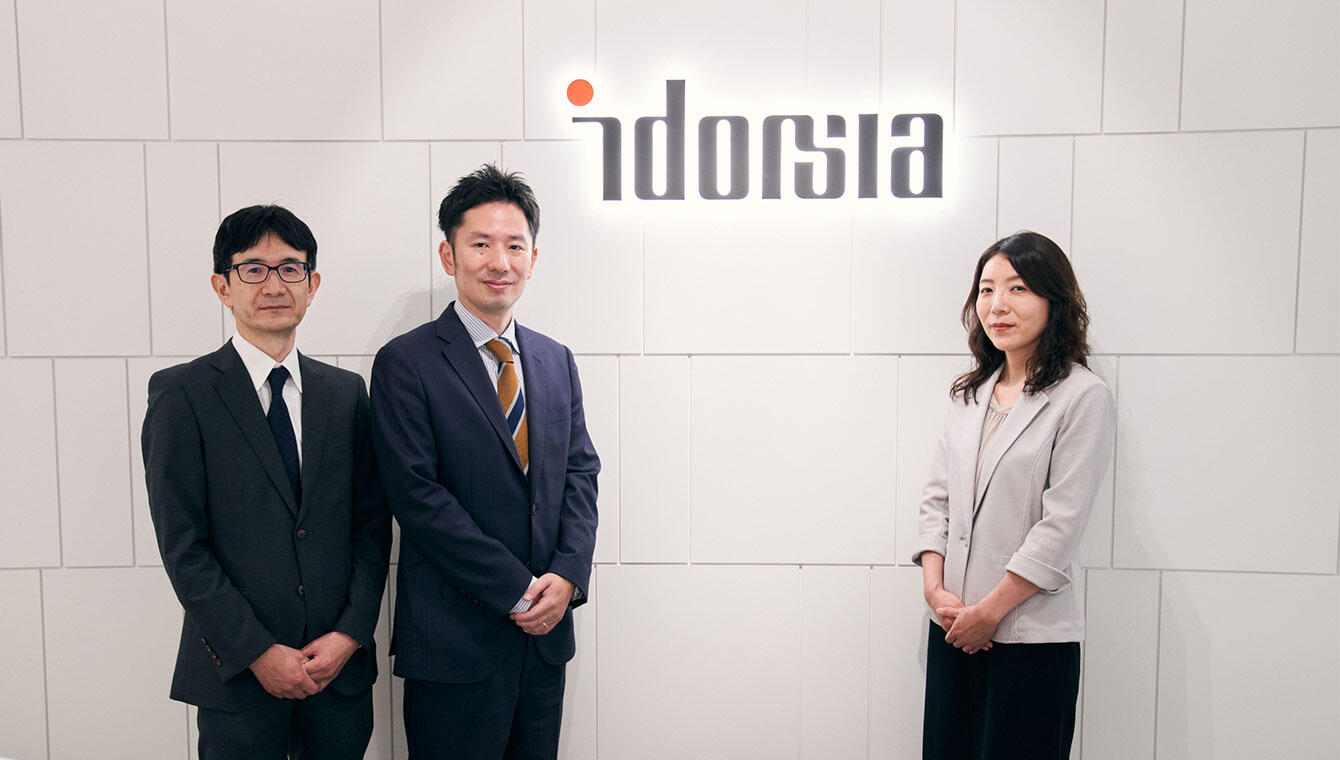
Idorsia Pharmaceuticals Japan Ltd.
Compatible with Global Requirements: Case Study of a Project to Build a Sales Management System Compatible with JD-NET
Medicine
ERP
Pharmaceutical & Medical Device Industries
SAP
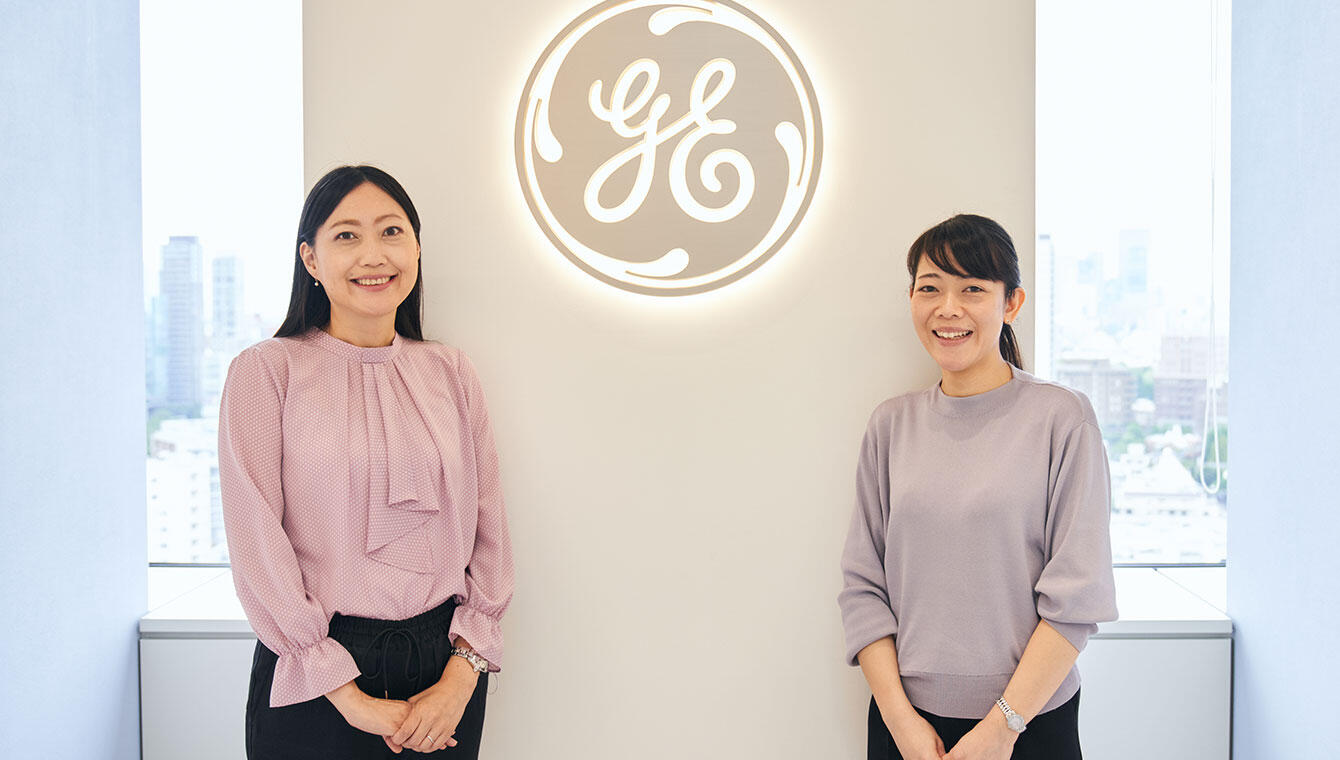
GE Healthecare Pharma Limited
Promoting Understanding among Global IT Teams: JD-NET-compliant Enterprise Resource Planning System Implementation Project Case Study
Medicine
ERP
Pharmaceutical & Medical Device Industries
SAP