Challenges
- When a malfunction occurs, there is inconsistency in the judgment of the people involved in communicating the information, leading to the malfunction becoming larger in scale.
- Periodic scheduled maintenance often results in equipment failures
Implemented Products/Solutions
WingArc 1st "MotionBoard"
Project Background
Human error is the root cause of equipment failure and poor quality. IoT is essential for a fundamental solution
Hefei Kobayashi Pharmaceutical was established in Hefei, China in 2013 as an overseas group company of Kobayashi Pharmaceutical Co., Ltd. The company produces raw materials for pharmaceuticals (herbal medicines) sold by Kobayashi Pharmaceutical and supplies them to Japan. The factory was completed and began full-scale operation in December 2016, making it a very young production base with an average employee age of around 30 years old. Due to the lack of experience that comes with being young, the company was struggling with frequent quality defects.
Kiminobu Okamoto, head of the company's production department, explained, "The direct cause that appears on the surface is equipment failure, but when we dug deeper into the true causes, we found that a significant proportion of them were due to human error and inconsistent judgment."
For example, there was a case where the temperature of a certain piece of equipment, which should have been maintained at a certain level according to the standard, fell a few degrees below the lower limit of the standard, but the staff at the site decided that "the temperature will rise soon, so let's wait and see." As a result, the fan malfunction caused by a clogged filter was overlooked, and the situation worsened. By the time the information reached the person in charge, it was too late to take action, and the entire lot of products produced in that process had to be discarded. "Similar troubles caused by people were occurring frequently as of 2019," Okamoto recalls. As long as we rely on human judgment, it will be difficult to fundamentally eliminate the quality defects mentioned above.
Hefei Kobayashi Pharmaceutical therefore aimed to solve this problem by building an IoT system. "Traditional measures based on the assumption that people are good and strengthening the reporting system alone were not enough to prevent human-caused troubles that occur several times a year, so we had to assume that people are bad. We constantly monitored the values of sensors placed on each piece of equipment, such as temperature and humidity, and visualized the operating status in real time, and also detected any abnormalities.
"We thought that if we could make the abnormality visible so that all employees, from workers to management, could see it at a glance when it was detected, we could speed up our response to the defect and minimize quality loss," said Okamoto.
The platform adopted to realize this IoT system is WingArc 1st's BI dashboard "MotionBoard," proposed by B-EN-G.
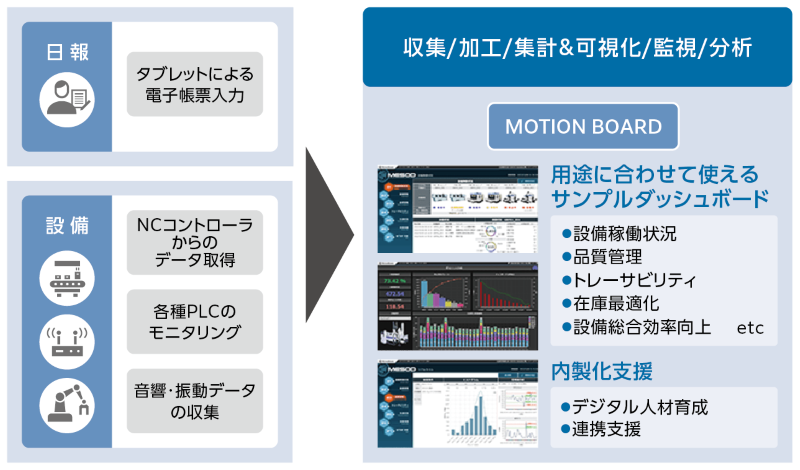
Project Background
The basic design of an IoT system capable of managing equipment status, processes, and maintenance was completed in about two months.
When asked why they chose MotionBoard, Okamoto explained, "Kobayashi Pharmaceutical Group and B-EN-G have been doing business with us for over 20 years in Japan and 10 years in China, so B-EN-G has a deep understanding of our business. B-EN-G proposed MotionBoard as the optimal solution, as it offers a high degree of freedom in screen design, has a proven track record in the manufacturing industry, and allows for effective global control."
Specifically, Hefei Kobayashi Pharmaceutical envisioned the following IoT system: First, on the top screen of the dashboard, the equipment status for each process (operating, stopped, warning, abnormal, abnormality response started, abnormality response in progress, etc.) is displayed in color. Furthermore, it will be possible to transition from the top screen to detailed screens for functions such as "process management," which visualizes problem locations on a control diagram, and "maintenance management," which visualizes the timing of part replacement based on the actual operating hours of each piece of equipment.
"B-EN-G was quick to respond to our request to 'visualize this kind of data in this way,' and presented us with a prototype screen. Thanks to B-EN-G's support, which helped us quickly realize what we wanted to do, we were able to complete the basic design of the IoT system in just two months," said Okamoto.
Implementation Results
System constructed in two phases Quality defects reduced to lowest ever number
The IoT system construction project, which kicked off in September 2020, was carried out in two major phases.
In Phase 1 up to December of the same year, a small-scale implementation was carried out, including as an experimental step, by visualizing process control items in a control chart for the processes where problems were occurring most frequently.
After making improvements to improve usability through actual use in Phase 1, and experiencing the benefits of the introduction, Phase 2 will expand the number of target processes and be expanded to other processes from 2021. In addition, a maintenance management item will be added to visualize the equipment operating hours of each process.
In this way, an IoT system that covers all processes for producing raw materials was completed, and Hefei Kobayashi Pharmaceutical began full-scale operation in 2022. After operation began, if the values of the sensors monitoring the equipment in each process exceed the specified thresholds, a warning or abnormality will be immediately displayed on the dashboard, and an alert will be automatically sent by email to the person in charge or responsible person.
This enabled the company to take swift action before equipment malfunctions occurred.
Regarding the results the company has achieved, Okamoto explains, "The number of quality defects in 2022 dropped dramatically. This also led to improved equipment operating rates, resulting in the highest production volume ever recorded." In addition, Tonomasu Tono, Deputy Manager of the Production Technology Section of the Manufacturing Department, also highly praised the effectiveness of the IoT system's implementation, saying, "When warnings or abnormalities occur in the equipment, we are able to quickly identify the cause by utilizing traceability."
The factory floor has also given positive feedback, saying, "We can now respond immediately to inquiries about the operating status of each piece of equipment." (Mr. Lee Chang-ho, Section Manager, Quality Control Division, Quality Management Department)
"It is now possible to check what changes have occurred in the data for each piece of equipment during the product production process, enabling us to achieve stricter quality control." (Li Ling, Section Manager, Production Technology Division, Production Department)
"In addition to being able to easily collect data from each piece of equipment, that data is stored as a log, so analysis can now be carried out very quickly," said Tan Shih-chiun, Quality Control Section, Quality Management Department.
"Data comparison, which was previously done manually, can now be done easily, simplifying the amount of work required," says Takeshi Den, facility manager.
Overview of the IoT system used at Hefei Kobayashi Pharmaceutical Co., Ltd.
Future Outlook
Aiming to evolve from corrective maintenance to predictive maintenance to become a "smart plant" that leads other companies' factories
While people in the field are becoming more familiar with IoT systems, there are also indications that further expansion of functions is required.
"The current dashboard focuses on monitoring and visualizing the operation of each piece of equipment, so I think quality control would become more efficient if we could provide a separate screen specifically for routine data analysis." (Sun Qian, Deputy Manager of the Quality Control Section, Quality Management Department)
"It's very convenient to receive email alerts when a warning or abnormality occurs, but we think it's necessary to take measures to prevent performance from deteriorating even as data volume increases." (Zhang Jiantao, General Affairs IT, General Affairs Department)
Taking these voices from the field into consideration, Hefei Kobayashi Pharmaceutical plans to further evolve its IoT system.
The company has set predictive maintenance as its next major theme.
"By shifting to a maintenance system based on the actual operating hours of each piece of equipment, we have been able to significantly reduce shutdowns due to breakdowns. However, from the beginning when we aimed to introduce an IoT system, we felt that it was necessary to visualize the signs that could lead to breakdowns. We will work to evolve from corrective maintenance to predictive maintenance," said Okamoto.
The company will continue to innovate, aiming to become a "smart plant" that can lead not only the Kobayashi Pharmaceutical Group but also other companies' factories.
Case study company introduction
Company Name | Hefei Kobayashi Pharmaceutical Co., Ltd. |
Establishment | October 29, 2013 |
Head office location | Hefei City, Anhui Province, China |
Business Activities | Processing and manufacturing of herbal medicine extracts (raw materials) and herbal medicines |
Company website | https://www.xiaolinyaoye.cn// |
*Please note that organization names, positions, numerical data, etc. in the article are based on the time of the interview and may have changed by current viewing.
Related Solutions
Relevant information and case studies based on solutions presented above.
Related Case Studies
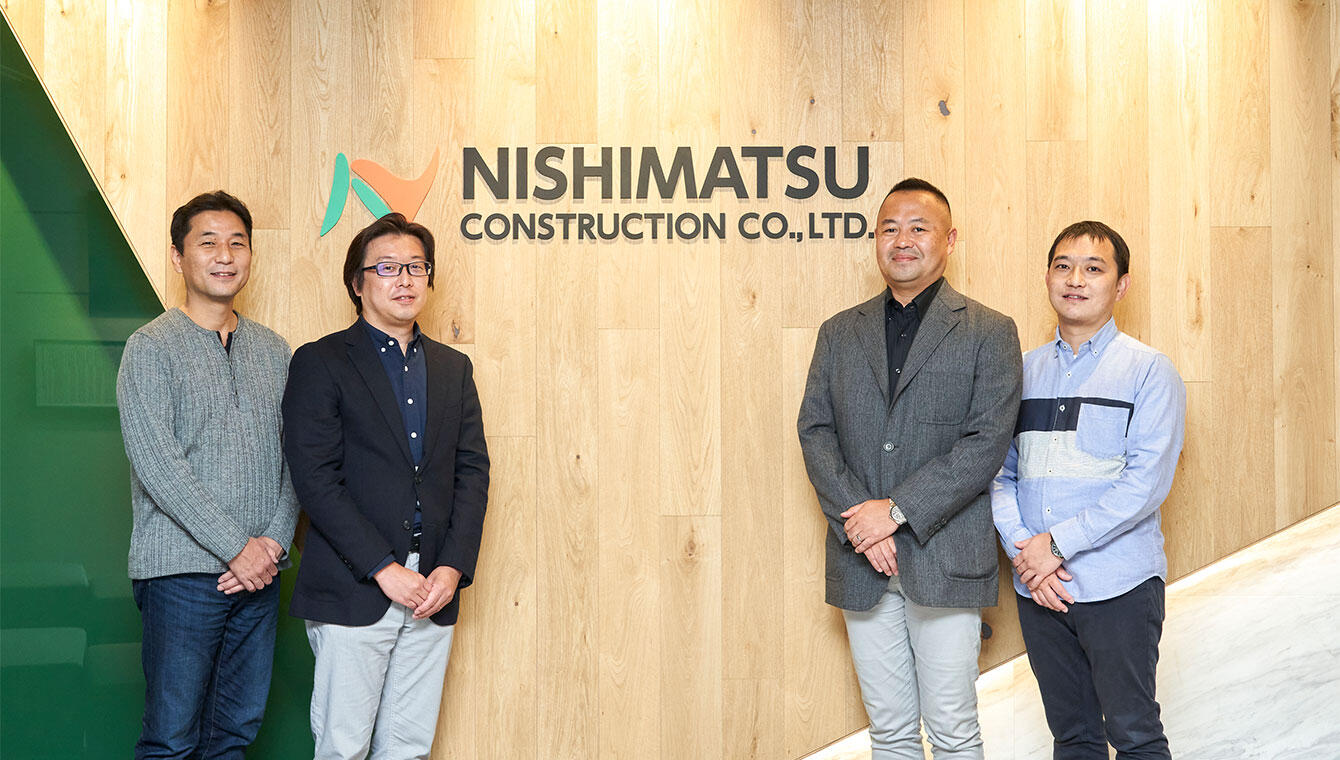
NISHIMATSU CONSTRUCTION CO.,LTD.
Data Utilization Infrastructure Development (MDM and BI Environment): Case Study for Promotion of Digital Transformation
Construction/Engineering
Data Management Platform Implementation & Utilization
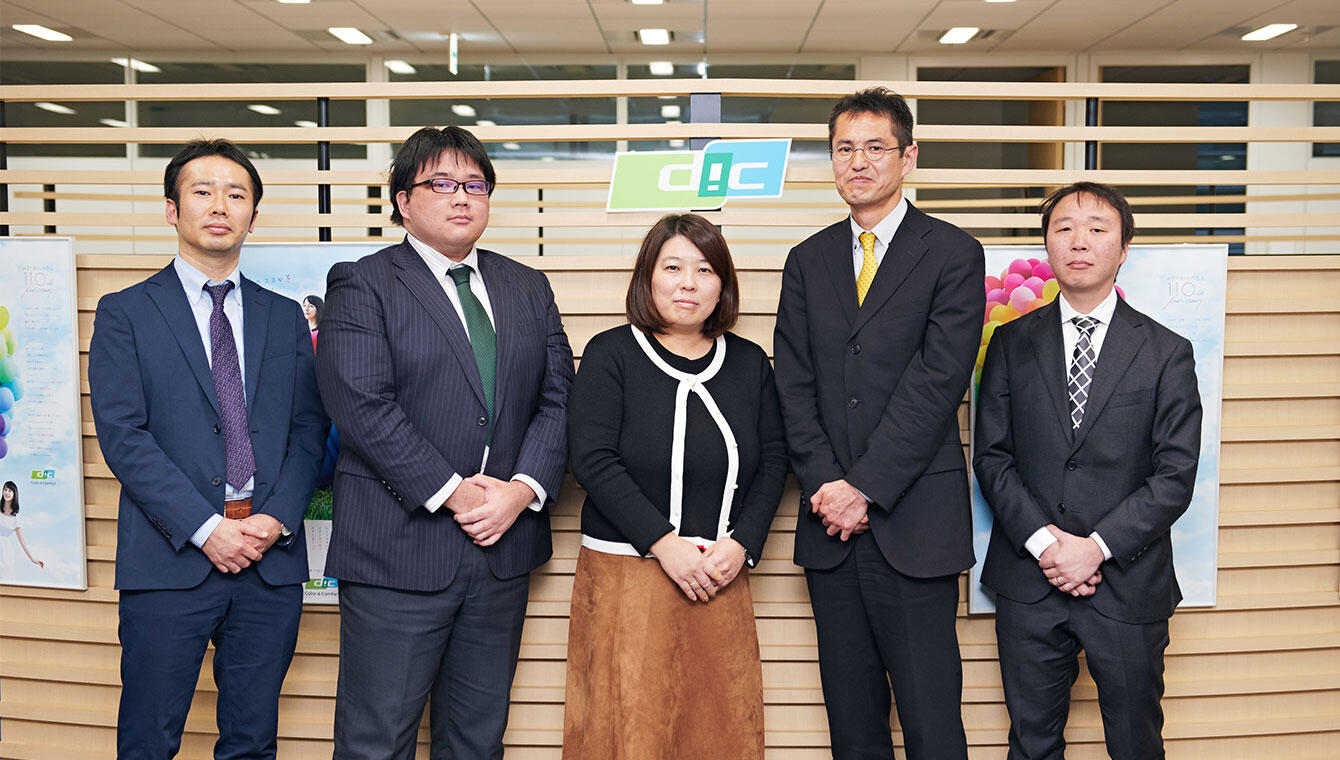
DIC Corporation
Achieving Advanced Performance Management and Improved Efficiency: Case Study of Building a Consolidated Global Performance Management Infrastructure
Chemical
Data Management Platform Implementation & Utilization
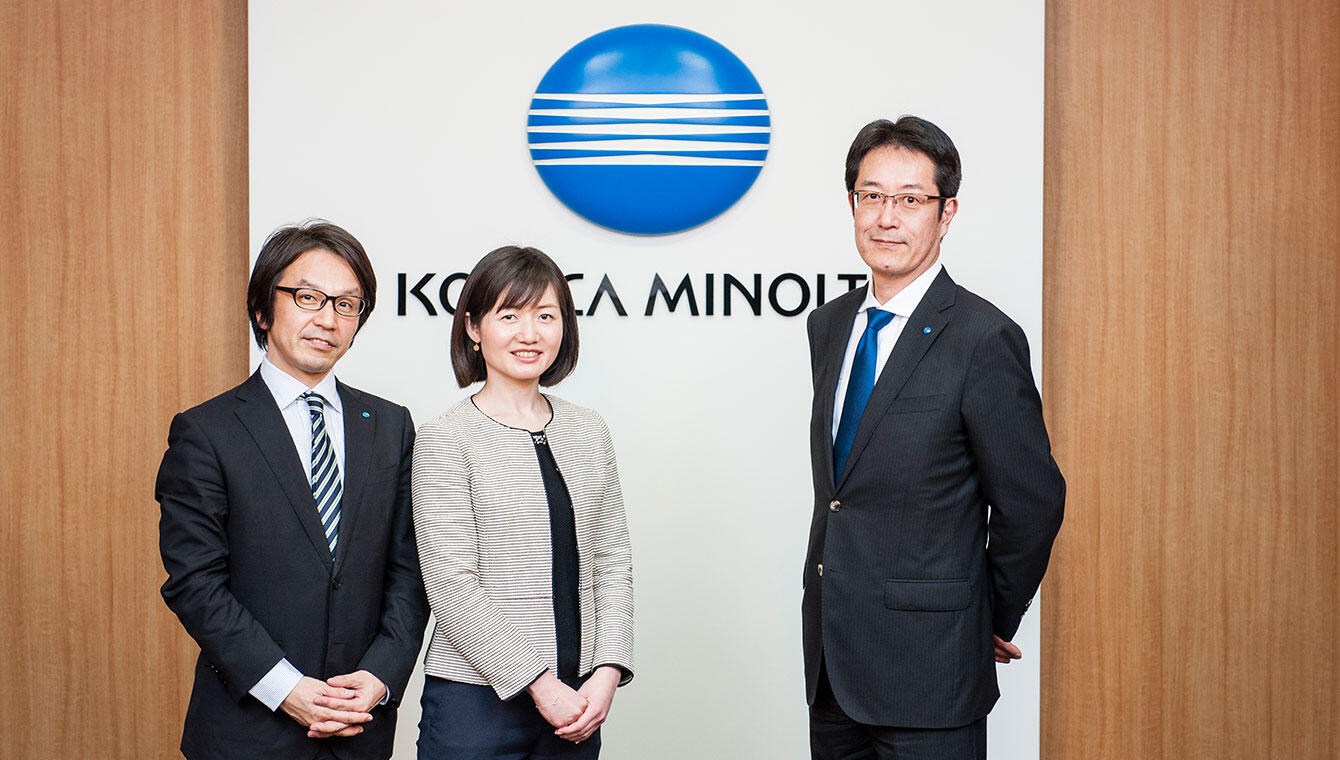
KONICA MINOLTA, INC.
Master Data Management (MDM) System Construction: Case Study Supporting Sophistication of Global Management
Precision mechanical equipment
Data Management Platform Implementation & Utilization